Technical Information
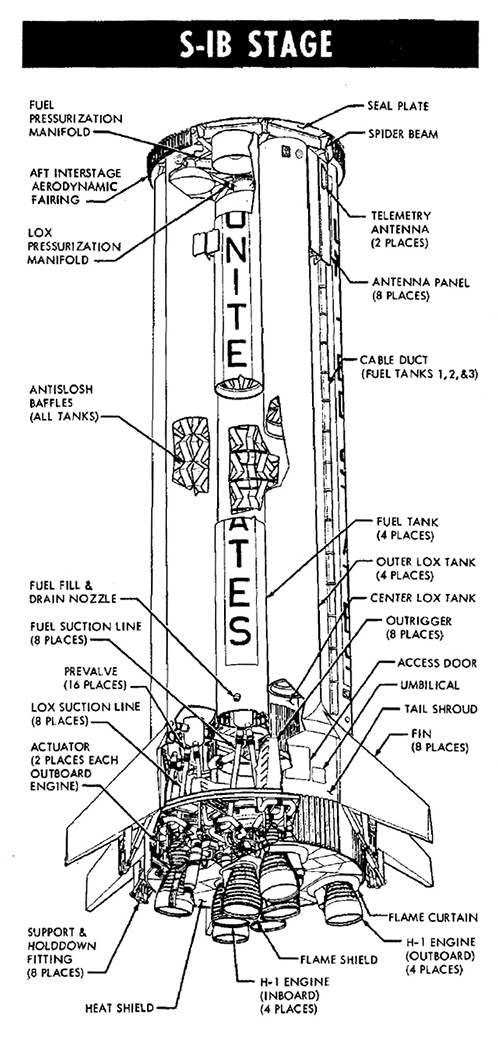
The Rocketdyne H-1, capable of generating 205,000 lbf (910 kN) of thrust, was a liquid-propellant engine burning a combination of liquid oxygen (LOX) and RP-1 (Highly Refined Kerosene). It was specifically developed for use in the S-I and S-IB stages of the Saturn I and Saturn IB rockets, where clusters of eight engines powered each stage.
The H-1 was part of a lineage of engines derived from the wartime V-2 ballistic missile designed by Wernher Von Braun. During World War II, North American Aviation (NAA) was tasked with examining several 59,600 lbf (264.9 kN) V-2 engines and converting their design from metric to SAE standards. This work led to the creation of NAA's Propulsion Division, which later became Rocketdyne.
The concept for the Saturn rocket emerged as a response to the U.S. Department of Defense's need for a heavy-lift vehicle capable of placing 10,000 to 40,000 pounds into low Earth orbit (LEO) or accelerating 6,000 to 12,000 pounds to escape velocity. Existing launchers could only lift around 10,000 pounds to LEO, making a larger design essential. In April 1957, Wernher von Braun assigned the preliminary design task to Heinz-Hermann Koelle.
Koelle's approach to reducing development time involved clustering fuel tanks from Redstone and Jupiter missiles on a single thrust plate, with multiple engines attached beneath it. To achieve the necessary thrust of about 1 million pounds, Koelle explored various engine options and identified Rocketdyne's E-1, a design introduced by George Sutton.
Like other early Rocketdyne engines, the H-1 featured a waterfall injector fed by turbopumps and used regenerative cooling, where fuel circulated through the engine to manage heat. Its combustion chamber consisted of 292 stainless steel tubes brazed in a furnace.
The H-1 was designed as a single-start engine. Although it could undergo multiple static test firings before a mission, it couldn't be restarted during flight, as some components, particularly the Solid Propellant Gas Generator (SPGG) used to initiate the turbopumps, were non-reusable. The SPGG functioned as a small solid rocket, ignited by 500V AC voltage. Once ignited, the SPGG generated hot gas, building pressure to 600–700 psi. A diaphragm then burst, releasing the gas into the turbine that drove the fuel turbopumps. This initiated the flow of fuel and oxidizer into both the gas generator and the engine, with the hot gases from the SPGG providing the energy to ignite the fuel-oxidizer mixture. The spinning turbopumps were then sustained by the exhaust from the burning RP-1 and LOX until engine shutdown.